The Six Sigma methodology gives businesses the tools they need to strengthen the capacity of their operational procedures. This improvement in performance and decrease in process variance contributes to the reduction of defects as well as an improvement in revenue, employee morale, and product or service
The term “Six Sigma quality” typically denotes that a process is tightly managed.
What is the difference between lean and six sigma
Lean encourages work uniformity and flow while Six Sigma focuses on eliminating waste (non-value added processes and procedures) and improving process control. The line between Six Sigma and lean has blurred, and the phrase “lean Six Sigma” is being used increasingly frequently since process improvement necessitates elements of both methodologies to produce fruitful outcomes.
Lean Six Sigma is an evidence-based, data-driven improvement methodology that places a higher priority on fault prevention than defect discovery. By lowering variance, waste, and cycle time and encouraging the adoption of work standardisation and flow, it boosts customer satisfaction and bottom-line results while giving businesses a competitive edge. Every employee should take part in it, and it applies whenever there is variance and waste.
- Lean uses less technical means, including as kaizen, workplace organisation, and visual controls, to achieve its goals, whereas Six Sigma frequently employs statistical data analysis, experiment design, and hypothesis testing.
- Lean places an emphasis on reducing waste, whereas Six Sigma puts an emphasis on reducing variation.
Application of six sigma
Organizations’ unique cultures and strategic business objectives can have a big impact on the Six Sigma deployment tactics used within them. An organisation has two fundamental alternatives following the decision to deploy Six Sigma.
- Execute a Six Sigma initiative or programme.
- Put together or construct a Six Sigma infrastructure
Execute a Six Sigma initiative or programme
With this approach, certain employees (practitioners) are periodically taught statistical tools and asked to apply them on the job as needed. If the practitioners require assistance, they may consult a statistician. Within an institution, there may be successes; however, such successes do not build on one another to encourage additional and better use of the tools and overall methodology.
When organizations embrace Six Sigma as a programme or effort, it frequently looks like they have just added a few new tools to their toolbox in an unorganised way through training sessions. Applying the tools as necessary to projects that have been assigned is one extension of this strategy. However, it’s crucial to keep in mind that choosing, managing, and carrying out initiatives are often not integral to the company.
It is better when Six Sigma training offers a process-oriented approach that teaches practitioners a methodology to choose the correct tool, at the right time, for a predetermined project instead of concentrating on the individual tools. This method of teaching Six Sigma usually includes four weeks of instruction spread across four months, with students working on their projects in the three weeks between sessions.
Put together or construct a Six Sigma infrastructure
It is better when Six Sigma training offers a process-oriented approach that teaches practitioners a methodology to choose the correct tool, at the right time, for a predefined project instead of focusing on the individual tools. This method of teaching Six Sigma typically involves four weeks of instruction spread across four months, with students working on their projects in the three weeks between sessions.
The most efficient method to get the most out of the time and money spent on Six Sigma training is to use projects rather than tools when implementing Six Sigma as a business strategy.
Numerous advantages can result from Six Sigma projects, including enhanced customer satisfaction, lower expenses, more profits, and more. Many Six Sigma Black Belts “handle four projects per year for a total of $500,000-$5,000,000 in contributions to the company’s bottom line,” according to the Certified Six Sigma Black Belt Handbook.
Five Principles of Lean Six Sigma
Experts recommend that you keep these 5 key Lean leadership principles in mind to help ensure the success of your LSS project.
1. Prioritize your customers
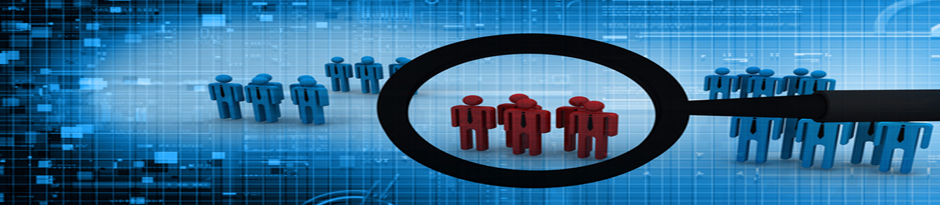
Delivering the greatest possible advantage to the client should be the main objective of any change you intend to execute. Early on, establish a clear level of quality that is determined by what the market or customers want.
2. Find your issue and pay attention to it
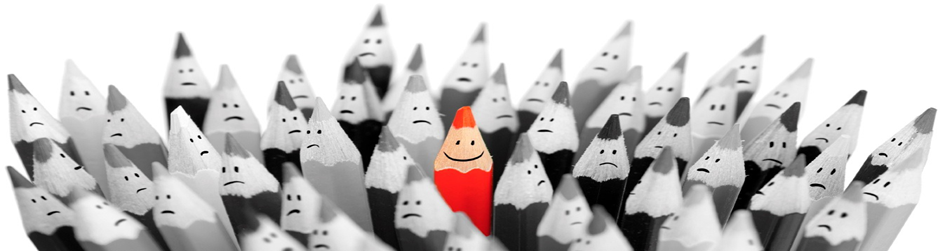
It’s simple to become distracted by the desired modifications during the retooling operations and lose sight of the original issue. Obtain information that identifies your specific problem area so you may focus just on improving that part of your company. The LSS procedure will probably be derailed by any attempt to significantly alter the business or the product.
3.Get rid of variance and obstructions
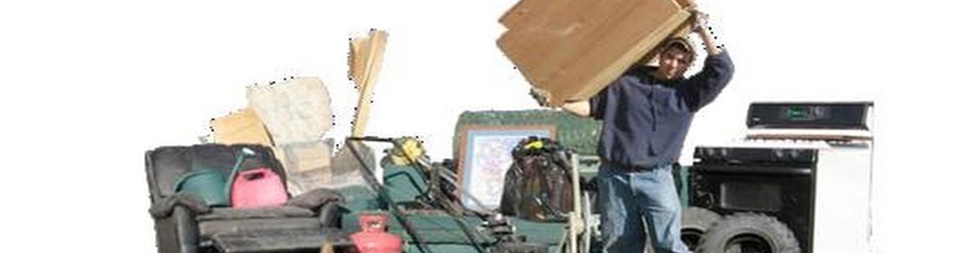
Once the issue has been located, you should start thinking about how to reduce the likelihood of errors. These gaps are frequently found in lengthy, complex procedures that offer a lot of possibility for error and waste. An good strategy to accomplish quality control and efficiency is by streamlining or eliminating these functions.
4. Clear communication and team member training
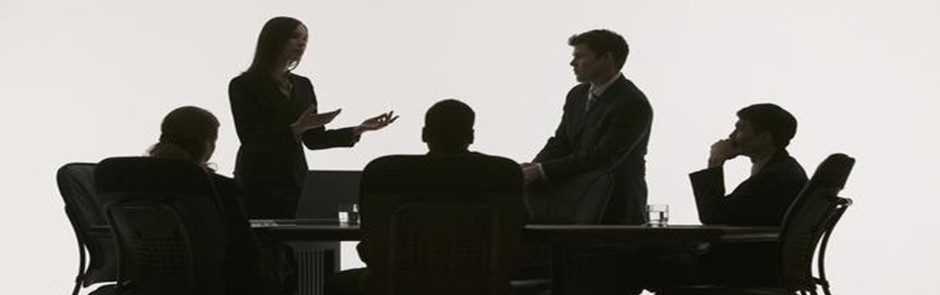
The basics of Lean Six Sigma demand that every team member understand LSS, be aware of the project’s objectives, and get regular updates on its status. The Six Sigma process can lead to significant change and calls for management to pay close attention. Advanced Six Sigma certifications are crucial for lowering the risk of project failure and guaranteeing the success of the entire process.
5. Be adaptable and receptive with flexibility
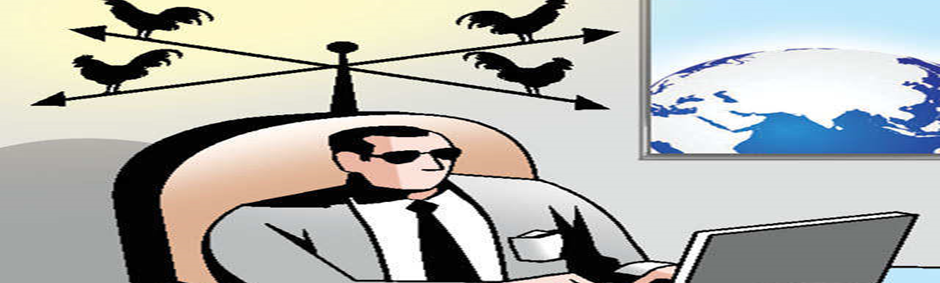
Lean Six Sigma and change go hand in hand. It is necessary to improve or eliminate a process or function that has been found to be flawed or inefficient. With LSS, sticking with a failed strategy is not an option. Change and change management can be difficult and uncomfortable, but they are a modest price to pay for the leaner, stronger, more competitive firm that every business leader aspires to.
Based on the categories, Six Sigma courses or certifications are as follows
1. Certified Master Black Belt (CMBB)
2.Certified Six Sigma Black Belt (CSSBB)
3.Certified Six Sigma Green Belt (CSSGB)
4.Certified Six Sigma Yellow Belt (CSSYB)
Benefits of Six Sigma Certification
There are many benefits to Six Sigma certification, including:
- Improved process efficiency and effectiveness
- Increased customer satisfaction
- Better decision-making and problem-solving skills
- Enhanced career opportunities and advancement
- Improved organization-wide quality management
Choosing the Right Six Sigma Certification Provider
When choosing a Six Sigma certification provider, there are several factors to consider, including:
- Accreditation: Look for a provider that is accredited by a recognized organization, such as the International Association for Six Sigma Certification (IASSC).
- Program offerings: Consider the range of programs offered by the provider, as well as their level of expertise in each area.
- Cost: Compare the cost of different programs offered by different providers to find one that fits your budget.
- Location: Consider whether you prefer an in-person program or an online program, and whether the provider has a location that is convenient for you.
- Support and resources: Look for a provider that offers a range of resources and support, such as training and support groups, to help you achieve your certification.
Types of Six Sigma Institutes
There are two main types of Six Sigma institutes: corporate institutes and third-party institutes.
Corporate Institutes
Corporate institutes are organizations that offer Six Sigma certification as part of their own quality management systems. These institutes typically offer a wide range of programs, including Six Sigma Green Belt, Six Sigma Black Belt, and Six Sigma Master Black Belt. Corporate institutes often provide additional resources, such as training and support, to help you achieve your certification.
Third-Party Institutes
Third-party institutes are independent organizations that offer Six Sigma certification programs. These institutes may specialize in a specific area of Six Sigma, such as Six Sigma Green Belt, or they may offer a full range of programs. Third-party institutes often offer more flexible scheduling options and may be able to provide more personalized attention to each student.
A List of Six Sigma Institutes:
Here is a list of some of the top Six Sigma institutes, both corporate and third-party:
- Six Sigma Academy: A leading third-party institute, offering Six Sigma Green Belt, Six Sigma Black Belt, and Six Sigma Master Black Belt certification.
- American Society for Quality (ASQ): A corporate institute offering Six Sigma Green Belt, Six Sigma Black Belt, and Six Sigma Master Black Belt certification.
- Villanova University: A third-party institute offering Six Sigma Green Belt and Six Sigma Black Belt certification, as well as a range of other quality management programs.
- Six Sigma Institute: A third-party institute offering Six Sigma Green Belt, Six Sigma Black Belt, and Six Sigma Master Black Belt certification, as well as a range of other quality management programs.
- Quality Management Institute: A corporate institute offering Six Sigma Green Belt, Six Sigma Black Belt, and Six Sigma Master Black Belt certification, as well as a range of other quality management programs.
- IASSC: The International Association for Six Sigma Certification is a third-party institute offering Six Sigma Green Belt, Six Sigma Black Belt, and Six Sigma Master Black Belt certification.
- Lean Six Sigma Institute: A third-party institute offering Six Sigma Green Belt, Six Sigma Black Belt, and Six Sigma Master Black Belt certification, as well as Lean Six Sigma certification.
These are just a few examples of the many Six Sigma institutes available. When choosing a Six Sigma institute, it’s important to consider your specific needs and goals, as well as the factors discussed in the article, such as accreditation, program offerings, cost, location, and support and resources.
Frequently Asked Questions about Six Sigma Certification Providers
- What is Six Sigma certification?
Six Sigma is a quality management system that helps organizations achieve their goals and improve their processes. Six Sigma certification is the process of becoming certified in the Six Sigma system.
- Why should I get Six Sigma certified?
There are many benefits to Six Sigma certification, including improved process efficiency and effectiveness, increased customer satisfaction, better decision-making and problem-solving skills, and enhanced career opportunities and advancement.
- What is the difference between a corporate provider and a third-party provider?
A corporate provider is an organization that offers Six Sigma certification as part of their own quality management system. A third-party provider is an independent organization that offers Six Sigma certification programs.
- What should I look for when choosing a Six Sigma certification provider?
When choosing a Six Sigma certification provider, consider factors such as accreditation, program offerings, cost, location, and support and resources
Read More about Six Sigma and Certifications
FAQs:
Is it important to have six sigma certification for all organizations?
No, it is not a mandatory requirement however, implementation of six sigma increases overall performance of organization
Pharmacareer team is a team of Experts from every department of Pharmaceutical industry having enriched experience. Experts have work experience of many multinational pharmaceutical industries worldwide.
One Reply to “Six Sigma and Lean Six sigma: Principle and Difference”