The Six Sigma methodology gives businesses the tools they need to strengthen the capacity of their operational procedures. This improvement in performance and decrease in process variance contributes to the reduction of defects as well as an improvement in revenue, employee morale, and product or service
The term “Six Sigma quality” typically denotes that a process is tightly managed.
How Six Sigma started
The bell curve was created in the 19th century by German mathematician and physicist Carl Fredrich Gauss. The bell curve established the idea of what a normal distribution looks like, which led to its early use as a tool for identifying flaws and faults in a process.
According to “The Complete Business Process Handbook: Body of Knowledge From Process Modeling to BPM Vol. 1” by Mark von Rosing, August-Wilhelm Scheer, and Henrik von Scheel, American physicist, engineer, and statistician Walter Shewhart developed this concept in the 1920s and demonstrated that “sigma imply where a process needs improvement.”
1. Explore the Genesis at Motorola: Delve into the birth of Six Sigma in the 1980s, when Motorola engineer Bill Smith pioneered a groundbreaking approach to minimize defects and enhance manufacturing processes. Learn how the term “Six Sigma” symbolizes precision and control, and how Motorola’s commitment to quality improvement led to the official launch in 1987 under the visionary leadership of CEO Bob Galvin.
2. Unpacking the DMAIC Framework: Understand the core principles of Six Sigma through the DMAIC (Define, Measure, Analyze, Improve, Control) framework. This structured, data-driven methodology is the key to Six Sigma’s success, focusing on statistical analysis to reduce process variation and achieve a level of excellence with only 3.4 defects per million opportunities.
3. From Manufacturing to Global Domination: Witness the expansion of Six Sigma beyond manufacturing as industry leaders like General Electric (GE) embraced the methodology in the late 1990s under the strategic leadership of Jack Welch. Learn how GE’s success propelled Six Sigma into diverse sectors, making it a global standard for quality management practices.
4. ISO Recognition and Standardization: Explore how the International Organization for Standardization (ISO) formally recognized Six Sigma in 2000, awarding it the ISO 18404 standard. This recognition solidified Six Sigma’s status as a structured management practice, encouraging organizations worldwide to integrate its principles into their management philosophies.
5. Lean Six Sigma Integration: Discover the evolution of Six Sigma as it integrates with Lean manufacturing principles. This powerful combination, known as Lean Six Sigma, optimizes efficiency by eliminating waste, enhancing process flow, and achieving optimal performance. Explore how this fusion has become a go-to approach for organizations seeking sustainable improvements.
Methodologies of Six Sigma
According to the 2005 book “JURAN Institute Six Sigma Breakthrough and Beyond” by Joseph A. De Feo and William Barnard, there are two main approaches to Six Sigma, both of which are made up of five sections.
DMAIC in Six Sigma
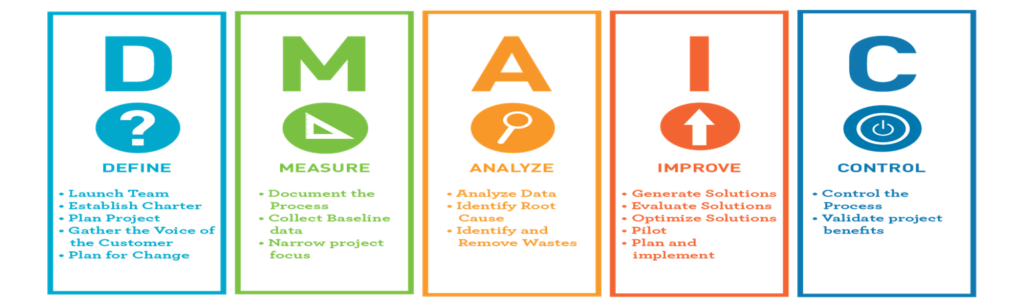
DMAIC: Define, Measure, Analyze, Improve, Control
- Define: Clearly articulate the problem, project goals, and customer requirements. Establish a project charter outlining the scope, objectives, and team members.
- Measure: Quantify the current process performance using relevant metrics. Identify key process characteristics and collect baseline data to assess the existing state.
- Analyze: Analyze the data to identify root causes of defects and variations. Use statistical tools and techniques to understand the relationship between process inputs and outputs.
- Improve: Develop and implement solutions to address identified issues. Optimize processes to meet or exceed customer requirements, using data-driven decision-making.
- Control: Establish controls to sustain the improvements. Implement monitoring systems, standardize procedures, and ensure ongoing measurement to prevent regression.
DMADV in Six Sigma
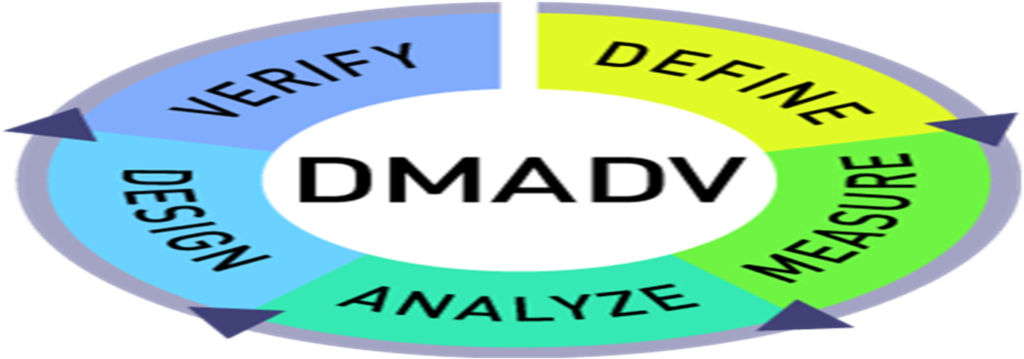
The DMADV method is typically used to create new processes and new products or services. The letters stand for:
- Define: Clearly define the project goals, customer requirements, and deliverables. Develop a detailed project plan, including milestones and resource requirements.
- Measure: Identify and measure critical-to-quality characteristics. Collect data to establish a baseline and understand current performance.
- Analyze: Analyze the data to identify key factors influencing the process. Prioritize critical factors that impact quality and performance.
- Design: Develop and design optimal processes and solutions based on the analysis. Implement changes and improvements to meet customer requirements.
- Verify/Validate: Verify the effectiveness of the new design through testing and validation. Confirm that the redesigned process meets customer expectations and achieves desired outcomes.
Five Whys in Six Sigma
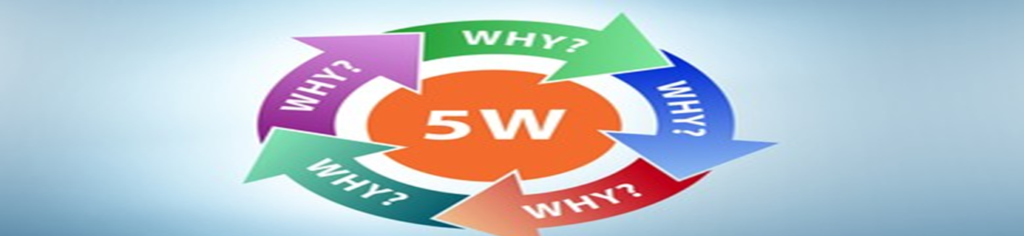
- Identify the Problem:
- Start by clearly defining the problem or issue at hand. This should be a specific and measurable problem that needs resolution.
- Ask the First “Why”:
- Ask why the problem occurred. This prompts an exploration of the immediate cause of the issue. The answer provides insights into the first layer of causation.
- Repeat for Four More “Whys”:
- For each answer obtained, ask “why” again to drill down further into the causes. Continue this process iteratively, aiming for at least five levels of questioning. The goal is to move beyond the symptoms and uncover the deeper, often systemic, root causes.
- Reaching the Root Cause:
- By the time the team reaches the fifth “why,” they should ideally have identified the root cause of the problem. The root cause is the primary factor that, when addressed, can prevent the recurrence of the problem.
- Implement Solutions:
- Once the root cause is identified, teams can develop and implement targeted solutions. Addressing the root cause directly helps in preventing the problem from reoccurring and contributes to sustainable improvements.
Example Scenario:
- Problem: Production line stoppage.
- Why 1: Why did the production line stop? – Because the machine malfunctioned.
- Why 2: Why did the machine malfunction? – Due to a lack of regular maintenance.
- Why 3: Why wasn’t the machine maintained regularly? – Because the maintenance schedule was not clearly defined.
- Why 4: Why wasn’t the maintenance schedule defined? – Because there was no established preventive maintenance program.
- Why 5: Why was there no preventive maintenance program? – Because there was a lack of awareness and training.
- Root Cause: The root cause is identified as a lack of awareness and training on the importance of preventive maintenance.
CTQ Tree in Six Sigma
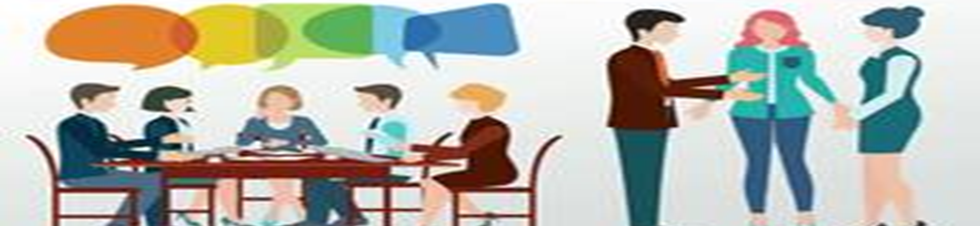
The Critical to Quality (CTQ) Tree diagram breaks down the components of a process that produces the features needed in your product and service if you wish to have satisfied customers.
- Define the CTQs:
- Begin by clearly defining the Critical to Quality characteristics. These are the key attributes or parameters that are vital for meeting customer expectations. CTQs are often derived from customer feedback, specifications, and business goals.
- Create the CTQ Tree:
- The CTQ Tree is structured hierarchically, resembling a tree with branches. The main branches represent the high-level customer requirements, while sub-branches break down these requirements into more detailed elements.
- Identify Sub-Characteristics:
- Each main branch of the CTQ Tree represents a major customer requirement. Break down these high-level requirements into sub-characteristics or sub-CTQs that contribute to meeting the overall customer expectation.
- Quantify and Measure:
- Assign specific metrics or measurements to each sub-CTQ. This step is crucial for turning qualitative customer requirements into quantifiable parameters that can be monitored and controlled.
- Link to Process Steps:
- Connect each sub-CTQ to the specific process steps or activities that influence it. This linkage helps in understanding how changes in the process can impact the critical characteristics identified by the customer.
- Prioritize CTQs:
- Prioritize the CTQs based on their importance to customer satisfaction and business objectives. This prioritization guides the allocation of resources and efforts in process improvement initiatives.
Example CTQ Tree:
- Main Branch 1: Product Reliability
- Sub-Branch 1.1: Component Durability
- Measurement: Mean Time Between Failures (MTBF)
- Sub-Branch 1.2: Product Lifecycle
- Measurement: Product lifespan in years
- Sub-Branch 1.1: Component Durability
- Main Branch 2: Service Responsiveness
- Sub-Branch 2.1: Response Time to Customer Inquiries
- Measurement: Hours or minutes
- Sub-Branch 2.2: Issue Resolution Time
- Measurement: Days or hours
- Sub-Branch 2.1: Response Time to Customer Inquiries
- Main Branch 3: Cost
- Sub-Branch 3.1: Product Cost
- Measurement: Cost per unit
- Sub-Branch 3.2: Service Cost
- Measurement: Cost per transaction
- Sub-Branch 3.1: Product Cost
The CTQ Tree serves as a valuable tool for aligning process improvement efforts with customer expectations. It helps organizations prioritize their focus on the aspects that truly matter to customers, fostering a customer-centric approach to quality management within the Six Sigma framework.
Root Cause Analysis
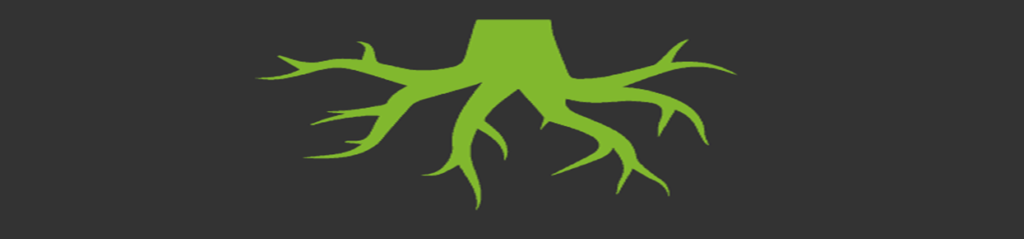
The goal of this procedure, which is similar to the Five Whys, is to find the actual source of a flaw rather than only treating the outward “symptoms” of it.
In order to provide the greatest products and services with the fewest defects, business processes must be streamlined using all of the Six Sigma tools and methodologies. Its widespread adoption by businesses throughout the world is proof of its outstanding success in the current business climate.
- Problem Identification:
- Begin by clearly defining the problem or undesired outcome. This should be a specific and measurable issue that hinders process efficiency or quality.
- Gather Data:
- Collect relevant data and information associated with the problem. This may include process documentation, historical data, customer feedback, and other relevant sources.
- Fishbone Diagram (Ishikawa or Cause-and-Effect Diagram):
- Utilize a Fishbone Diagram to visually represent potential causes of the problem. The main categories on the diagram typically include People, Processes, Machines, Materials, Measurement, and Environment (the 6Ms). Brainstorm with a cross-functional team to identify possible causes within each category.
- 5 Whys:
- Apply the “5 Whys” technique to delve deeper into the identified causes. Ask “why” repeatedly to uncover successive layers of causation. The goal is to reach the root cause, which is the factor that, when addressed, will prevent the problem from recurring.
- Pareto Analysis:
- Prioritize the identified causes using Pareto Analysis. Focus on the factors that contribute most significantly to the problem. The Pareto Principle, or 80/20 rule, suggests that a significant portion of problems often results from a small number of causes.
- Data Analysis Tools:
- Employ statistical tools and techniques to analyze the data associated with potential causes. This may involve hypothesis testing, regression analysis, or other statistical methods to validate the significance of identified factors.
- Verify and Validate:
- Confirm the root cause(s) through testing and experimentation. Implement changes based on the analysis and observe the impact on the problem. This step helps ensure that the identified causes are indeed the root of the issue.
- Implement Corrective Actions:
- Develop and implement corrective actions to address the root cause(s). These actions should be designed to prevent the problem from recurring and may involve process improvements, policy changes, or other targeted interventions.
- Monitor and Control:
- Establish monitoring and control mechanisms to track the effectiveness of the corrective actions. Continuous monitoring ensures that the implemented changes are sustained over time.
Six Sigma Levels and roles/ Certification type/ Belts

- White Belt:
- Role: Entry-level understanding of Six Sigma concepts.
- Responsibilities: Basic awareness and support for Six Sigma initiatives.
- Certification: Typically involves a short training program or workshop.
- Yellow Belt:
- Role: Team member or support role.
- Responsibilities: Basic understanding of Six Sigma tools, participation in improvement projects.
- Certification: Entry-level certification, often after completing a Yellow Belt training program.
- Green Belt:
- Role: Project leader or member of a Six Sigma project team.
- Responsibilities: Lead or contribute to improvement projects, analyze and solve problems using Six Sigma methodologies.
- Certification: Comprehensive training and examination on Six Sigma principles and tools.
- Black Belt:
- Role: Project manager or leader of Six Sigma projects.
- Responsibilities: Lead complex improvement projects, mentor Green Belts, and analyze and implement solutions.
- Certification: Intensive training, project completion, and passing a certification exam.
- Master Black Belt:
- Role: Expert and mentor in Six Sigma methodologies.
- Responsibilities: Provide strategic direction, mentor Black Belts and Green Belts, and oversee the overall Six Sigma program.
- Certification: Advanced training and significant hands-on experience, often with a track record of successful projects.
- Champion:
- Role: Senior executive or manager.
- Responsibilities: Provide leadership and support for the Six Sigma program, align projects with organizational goals, and ensure resources are allocated appropriately.
- Certification: Not a specific certification, but Champions typically receive training on Six Sigma principles and methodologies.
Additional Certifications:
- Lean Six Sigma: Integration of Lean principles with Six Sigma methodologies. Certifications may include Yellow Belt, Green Belt, and Black Belt in Lean Six Sigma.
- Design for Six Sigma (DFSS): Focuses on designing new processes or products that meet or exceed customer expectations. Certifications may include Green Belt and Black Belt in DFSS.
- Master Black Belt in Leadership: Emphasizes leadership and strategic skills in addition to deep Six Sigma knowledge.
Certification Bodies: Various organizations offer Six Sigma certifications, with the most well-known being:
- American Society for Quality (ASQ): Offers certifications for Yellow Belt, Green Belt, Black Belt, and Master Black Belt.
- International Association for Six Sigma Certification (IASSC): Provides globally recognized certifications.
For more articles, Kindly Click here.
For pharmaceutical jobs, follow us on LinkedIn
For Editable SOPs in word format contact us on info@pharmaceuticalcarrier.com
For more information kindly follow us on pharmaguidelines.co.uk
For Basics and differences between six sigma and Lean Six sigma kindly visit:
Pharmacareer team is a team of Experts from every department of Pharmaceutical industry having enriched experience. Experts have work experience of many multinational pharmaceutical industries worldwide.
One Reply to “Six Sigma Belts and levels | Certification types in Six Sigma”